Now it's time to work on the fenders. Picked up a spool gun for my welder and I'm going to fab some inner wheel wells for the hi-line fenders. I will also be replacing the weak grill struts with some 3/8" turnbuckles from the grill to the hoop cross bar.This should sturdy things up. These GenWrong fenders have been an issue from day one and need some reinforcing. The drivers side will also have an incorporated cold air intake box.
Ready for fab.
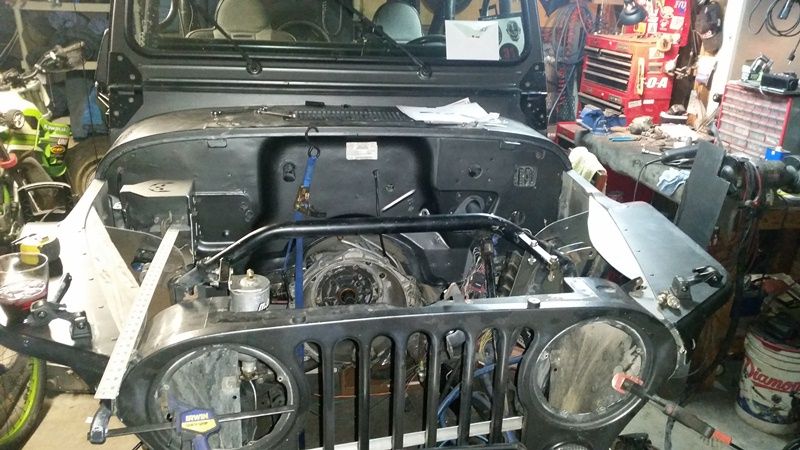
Some 6061 and perforated aluminum for the inner fenders.
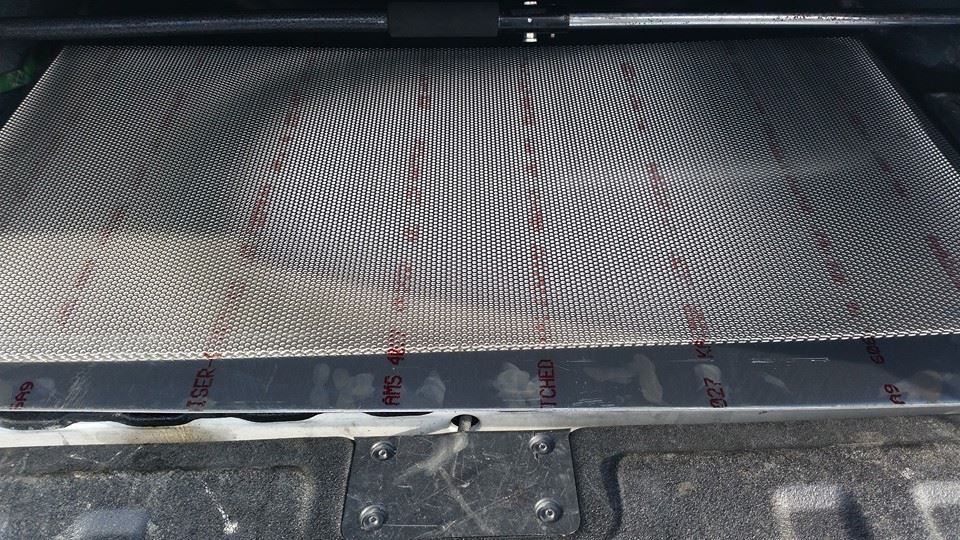
Also staring to work on the wiring.
All the crap on the firewall shown here.
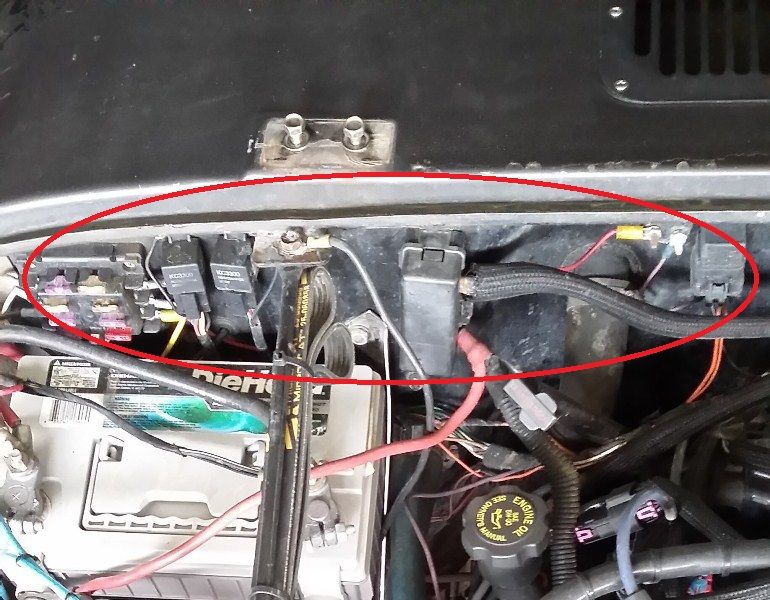
Will be incorporated in to this small waterproof box.
Ready for fab.
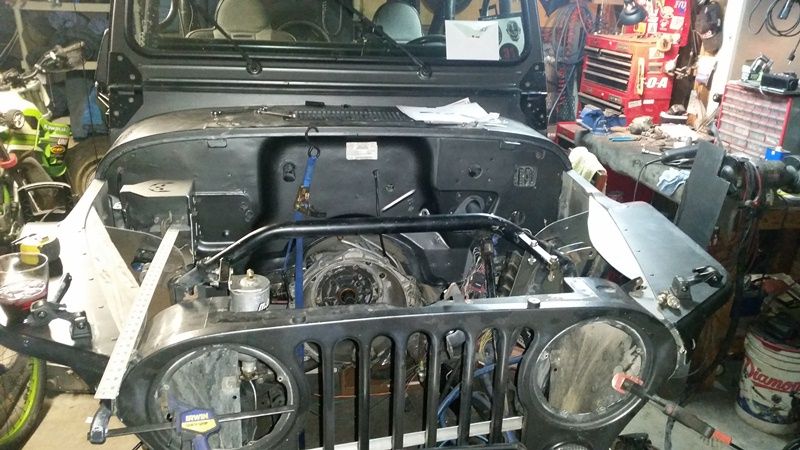
Some 6061 and perforated aluminum for the inner fenders.
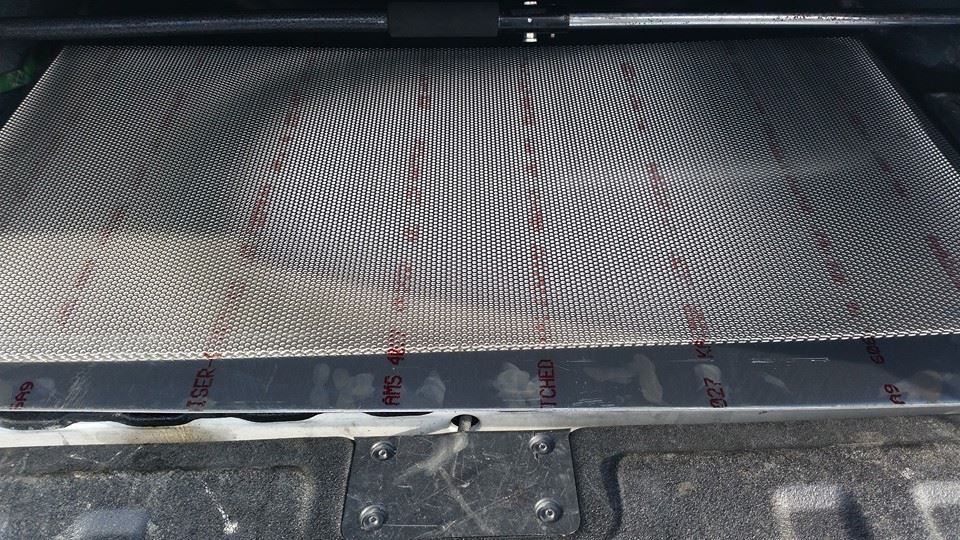
Also staring to work on the wiring.
All the crap on the firewall shown here.
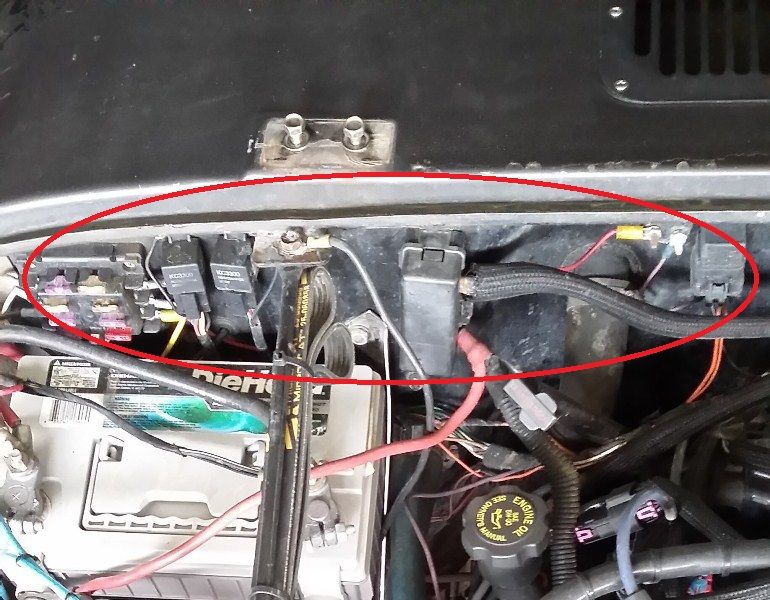
Will be incorporated in to this small waterproof box.
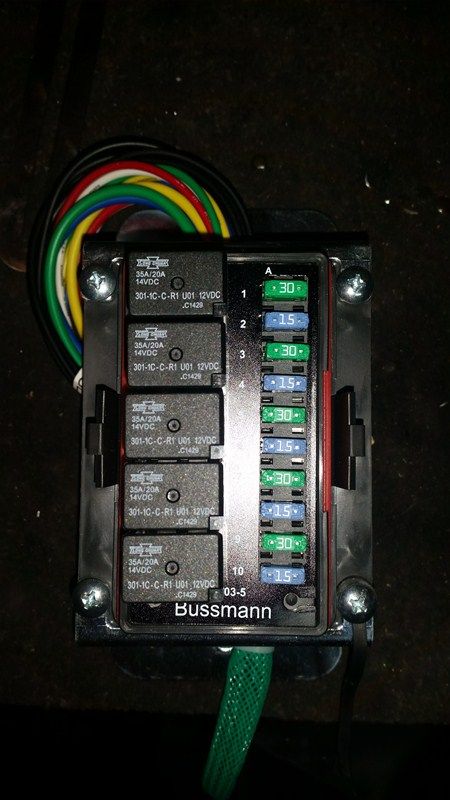
Comment